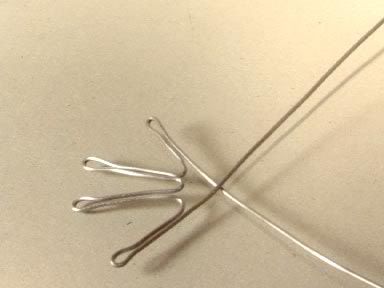
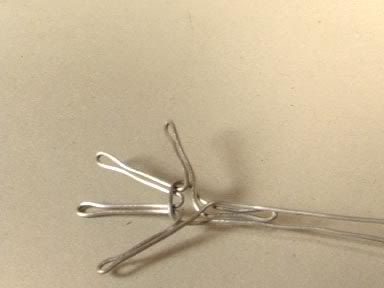
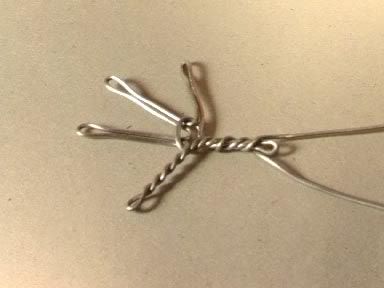
And here's the promised writeup about the problem I discovered with the thread-wrapped wire method of armature construction.
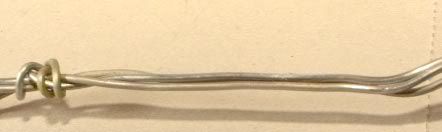
See... this pic shows the most comfortablest way for three wires to nestle together.... the cross-section would look triangular. And I've found three 1/16" Almaloy wires is a perfect combo for most parts of the puppets I'm making. The triangular configuration is a thing of beauty and much economy.... it's the way they naturally want to lay anyway when you start wrapping... it's a lot harder to get them to lay out side by side (flat cross-section like a ribbon).
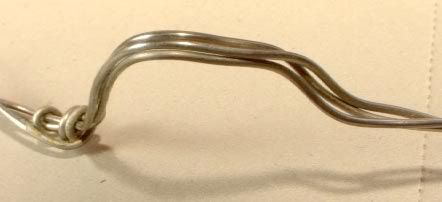
BUT... Here's the problem with it. All I did was bend the wire-thing here, and see what happened? The wire that was behind the other two popped out between them, and now it's gone from triangular profile to flat profile. This is what happens inside the puppet when you bend a joint if the wires were in triangular configuration to start with... and to complicate matters, even if you originally made it in flat configuration, it will shift from handling. In other words, it's constantly shifting between the two configurations...... and this causes stress. I can tell by the popping sound I hear when it happens! At first I didn't know what was going on... I though something was breaking, but obviously nothing was.... so I examined it closely and bent it back and forth a few times, and then I saw it happen. See, the problem is that when the wires are in triangular configuration and you bend them, the wire in the back would need to stretch... or else pop through between the other two. When you go with the good old fashioned twisted wire method, they're sort of springlike, so the back one actually can stretch a bit, and the front ones can compress a little too. Crazy stuff!
This doesn't mean the thread-wrapping method is crap or anything... it's just a different alternative. I believe both methods have their strengths and weaknesses (a bit too tired to pontificate any deeper on it right now). And the popping-through thing doesn't jhappen all the time, possibly it's only on certain joints depending on how they were made, I'm not sure. It's just something I noticed and wanted to share.
12 comments:
Ah! The popping wire phenomena is a fascinating observation! Thank you so much for sharing that one. :-D
That's an interesting hand design -- particularly the loop that goes between fingers. Is this design your own invention? Or did you learn it somewhere else? ...I saw something similar at Bent, but I couldn't get a good enough look to figure out exactly what was going on with the individual strands.
I did figure out, though, that they use thread-wrapped florist wire for hands. 28 gauge, I think. I'm told that it can be purchased at Michael's, but haven't gone looking for it yet. [I'm not giving away any secrets here; if you go to the Bent website and look at their "making of Rubberband Man" video, there's a brief shot where you can see what I'm talking about.]
A trick that I learned for making hands, while taking that sculpting class from Kim Graham... Although this is for more for making sculpting armatures than animation armatures... Get yourself a small hook. File the screw end of it so that it has three flat faces. Now it will fit in the chuck of a power drill. Hook the hook into a fingerloop and twist.
Kim also had us putting a second loop of wire between the fingers, so there'd be four strands in the wrist. It was a quick and elegant design. Although, we were using copper wire -- also 28 gauge, I think. [Oh, and it was the beautiful red annodized (?) stuff that gets used for making magnets. It stood out really nicely... Boy I'd like to get my hands on a spool of that.]
I think this was a majot progress day, Mike. That tut of the hand in each stage really helps me to copy, I mean learn. I'm not sure I follow what you're saying about the wrap method vs. not as I don't know the difference between the two. If you wrap does it prevent the stresses of repetitive movment on the wrist wire trio?
I just made up the hand design... not a design so much as just spur of the moment invention. The main thing was to come up with a multi-tiered wrist piece, so part of it can butt up against the end of the forearm 'bone' and I'd still have two longer parts to secure against the sides of the forearm. Maximum area of joinage.
The loop I add at the end (in the palm area) is basically for two reasons... to help secure all the fingers together to an extent (that will be more secure when I add a block of epoxy putty there later) and also to have those two extra pieces of wire to lay alongside the forearm.
Floral wire would be nice for the cloth wrappage... especially if I end up making some of the arms in silicone... it would save me having to wrap string around the fingers. But that florist's wire is steel, and not as flexible as almaloy. Would still work though.
Shellsies,
most people don't bother to wrap silk thread around the wires when making an armature... instead they just twist the wires together to bind them into one unit that bends coherently. Laying them straight alongside each other and wrapping with thread is an alternative method. Both methods have their advantages. When I first learned about the threadwrapping method I was all gung ho about it... haven't gone back since (until making these hands).
I don't get your question though... the wrist wires aren't a trio - it's a quadro, and the "stresses of repetitive movement" sounds like you're referring to the thread-wrapped parts, as I described in the post above.... that doesn't happen with wire-twisting.
You said there were three wires in the photos and by gum all I can see are three, where's the fourth?
Break it down for me:
wrist wires flat; get wrapped; point of wrapping is:
wrist wire triangle: no wrap; point of triangle is:
Thank you (see it's like you've never left SMA)
Ok.... to try to explain more clearly:
It's not the wrist that's a problem at all. That has 4 wires, which are twisted (not thread-wrapped). Check the second of the pics in this post and you'll see the 4 wires before I twisted them together.
The joints I'm referring to (with the popping problem) are in the shoulder and elbow. The ones that are wrapped with thread.
Maybe that's the source of your misunderstanding? Maybe you thought I was talking about the wrist joints?
The point of wrapping the wires is just to bind them all together into a single flexible form, so when you bend say an elbow back and forth a few times you don't have them coming apart in different directions, making the elbow look swollen and making it hard to animate. In the twisting method this isn't a problem.
Oh wait... I just though of what might be throwing you... my demo joint? The last pair of pics I posted is just strictly a quick demo. I left it unwrapped just for convenience's sake. It's only intended to demonstrate the way the wires force themselves into flat configuration when bent.
Now maybe we're on the same page?
Damn spam! Gotta get me some Spamaway!
I'm not sure if I understood correctly your wire problems, (my english is good but maybe sometimes not that fluent). As we usually use latex foam for arms and fingers we make the hands in quite a different way. Only one wire per finger and then cover them with sowing tread (sorry about the terms, donte remember another word for it), so thar it is a litlle sronger and also for the latex to mix with it, not allowing it to move. For the arms, we usually twist them with a screwdriver (great results, low velocity of course) and then use epoxi for the "bones". Really loved the way you make the hands!
Yeah, I guess most people wouldn't understand.... it's pretty technical stuff and I don't think anyone would really understand unless you've made armatures using the thread-wrapping method. I probably didn't do a very good job explainign it either. Basically I only wrote that here as kind of a note to myself and for the benefit of anyone who has tried that technique or might want to try it.
It isn't a major deal or anything... i don't know if it's causing lots of stress on the wires, it just makes this clicking or popping sound when they shift. I'm already devising a modified system in my head that I'll try for the lower bodies.
Menir, thanks for sharing your techniques! I'm thinking of casting some of these arms in silicone, and for those I would also wrap the fingers with thread. As I understand it you need to actually rub a thin coat of silicone into the thread first to help it adhere, then when you pour the mold full the rest will stick to that first layer... otherwise you can have problems with the silicone coming loose.
But right now I don't even want to think that far ahead.... every time I do I just sigh and shake my head. So much work still to go on these puppets! And when I get them done, then I start on the set and all those little bottles and cups and mugs..... aaaaauuuuuuuuuugghhhhh!!!!!!!!
m_) I am doing my best at deciphering how to create a hand as great as yours...
m_) I see figure 1...follow...then figure 2..LOST!..I mean, I get it ..I just keep wondering how do you twist it in such a way so it still looks right. Damn it...stupid crash course english of mine...
m_) I wish I mastered descriptive verbs and all...
Post a Comment