Veronica is a barmaid at Cosmo's tavern. That's Cosmo beside her. Oh, he now has the lower body I originally made for Huck... the weird long torso thing works better on him (partly because he'll be wearning an apron and standing behind the bar most of the time!).
I'd like to walk you through the process I use to make the lower bodies. There are a few techniques I want to share that I've picked up over the years... and trust me, I made a lot of mistakes along the way and learned a lot of what not to do!

For starters, here's the way I lock the wires into the little pieces of tubing:
I always like to make some kind of hook or loop in a wire where it will be embedded in epoxy - this creates an actual physical bond, a mechanical join that is much stronger than the adhesive itself. A straight wire embedded in a block of epoxy can easily turn or even pull straight out. I defy anyone to spin these wires inside the tubing, or to pull them out!
Every bend you put in a wire should serve some purpose... often it can serve two or more at the same time. By making these two little hooks I effectively double the thickness of the wire inside the tubing, almost filling the available space, as well as creating that physical lock.

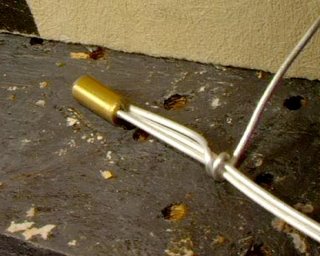
I wrap the short wire around at the point where the pelvis is to be located. I only touch the wire with my fingers when I'm bending and twisting it.... you don't want to put any nicks in it by working it with pliers or anything. Every nick is a weak point where the wire can easily break during animation. But it is ok to use pliers in areas where the wires will be embedded in epoxy, like here or when I made the loops. No way I could do THAT with my bare handses!

I mark the length I want a leg to be and place a thumb nut there that has been filed around the groove to rough it up so the epoxy can find purchase.
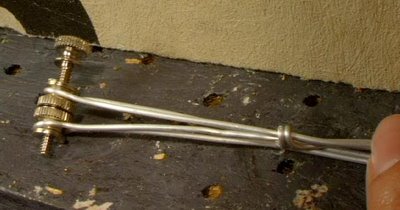
This is my clever little trick to make sure the legs are exactly the same length (just thought of it now... this is the first time I've used it). I used a thumb screw to secure another thumb nut to the first one, then wrap the wire around it the same way. Once this is done I remove the screw.
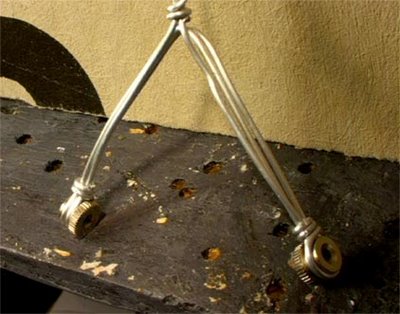
Hope you can make out what's going on here. What I did was bend each wire down the other leg, so each leg now has three wires. I wrapped the wires around the thumb nuts... there's just enough room for two loops of wire there. Then I tie the wires off as you can see and cut off the excess making sure to use the pliers to tuck the cut end nicely down where it won't poke out and cause any trouble. It will be embedded in kwikweld in a moment. All that's left then is to kwikweld the thumb nuts securely in place and mix up a blob of epoxy putty for the pelvis block. I use a steel filled epoxy putty that happens to look just like the (also steel-filled) kwikweld. Once everything is all set up then I twist the legs and the spine, which has the effect of tightening everything down nicely. Obviously this was for a puppet that doesn't have the rectal tiedown for barstool attachment. If it did I would have attached the thumb nut to the short wire at the beginning of the process. I could have made this in about 15 minutes, but making the tutorial added about an hour! I've got two more bodies to make... I'll see if I can get them done yet tonight before hitting the sack. Really getting tired of messing with all this wire and goop!
Update:
Finished the last two... now all the armatures are complete except for the secret puppet.
10 comments:
Oh Come on... Show the secret puppet, show the secret puppet, show the secret puppet!
This production fest is really showing results, bend on!
This is fantabulous, Mike. I'll follow along as best I can when I'm at that stage. Question: is kwikweld and epoxy putty toxic to touch when blending and or in its fumes? If so, (you best be wearing proper gear or else my wrath upon you) when I make mine, could I at all come up with a not as good but serviceable non-tox version? Like, don't laugh, a blob of hotglue?
Mike -- I LOVE it! Thank you for taking the extra time!
Shelley -- I know someone who does the hot glue thing for his puppets -- but they're smaller than your scale, and only use florist's wire for the armature.
If you really want to avoid the tox, you might be able to drill holes in blocks of wood for the body blocks, weaving the wire through. Nick Hilligoss has occasionally done this -- you can see photos on his site. For leg and arm bones, using thin wire to affix a nail or wooden dowel can work (sort of like a splint).
I can't promise that these strategies will be fully adequate... But if no-tox is priority #1, I think that's the avenue you'll want to explore.
Thanks for taking the extra time for the tut Mikey....now give up the secret or Buster sleeps wit da fishes :)
Thanks Svensters, yes, non-tox primo importante por moi.
I ain't got nothing else to say, I just wanted to type out my new non-rotated emoticon:
\(^]^)/
`º U º
Shelley, that's.....almost obscene....:) maybe its just me....
Hot glue? Man, maybe not toxic per se, but so much more dangerous! I've used it before for securing bones... it's kind of flexible and hard to work with.... unless you want flexi-bones you'd definitely want to tie a bone in place first. Expect lots of finger-burns.
I don't worry about the toxicity of epoxies.... they've never given me any toxic 'feel' if you know what I mean, not like solvents etc. I do wear latex gloves to work with the putty, which makes it hard to work it effectively. Sometimes when it's firming up and I still need to get a little better dexterity before it goes rock hard I'll whip off the gloves and finish it with my bare hands. Problem with that is you get that powder all over! Tip... wipe your hands quickly on your pants first.
There's just nothing more effective than epoxies for this kind of work.
Oh, and the kwikweld I don't touch... just mix it up and apply with a tool.
Pants wiper. (me too, who needs nakins?) I weld a glue gun every day, tough finger tips by now. I'll have to speriment with blocks, putty n'stuff. I have a cartridge respirator, maybe I could do that part on the roof (without a lock on the door.)
I see what you mean there J, on the drawing above, I meant it as a G-rated happy face however. (Obvi, bc it's me.)
One more tip about hotglue... don't use it on anything that will be going into the oven later (like a foam latex puppet or anything this will have polymer clay parts). I used it once on a aculpture armature, and it melted and ran out all over everything. Maybe not so bad.... it ended up being hollow and lighter.
Post a Comment